Washing machine motor end caps stamping production
Washing machine motor end caps and explains the transfer die stamping production process
In today’s highly competitive appliance market, the performance and longevity of washing machines depend not only on advanced control systems and energy efficiency but also on the reliability of mechanical components. One critical component in a washing machine’s motor is the end cap, a precision-engineered part that serves multiple functions such as protecting internal components, ensuring proper alignment, and dissipating heat. The manufacturing of these motor end caps has evolved significantly over the years, with transfer die stamping emerging as a key production method. This report offers an in-depth exploration of washing machine motor end caps and the transfer die stamping production process, detailing design considerations, manufacturing steps, quality control methods, and innovations in production technology.
Understanding the Washing Machine Motor End Cap
The motor end cap is an essential component in the assembly of washing machine motors. Often made from metal such as cold-rolled steel or aluminum alloys, the end cap is designed to seal the motor housing, support bearings, and sometimes assist in heat dissipation. Functionally, the end cap provides a structural interface between the motor’s rotor and the stator, protecting the internal windings and mechanical parts from dust, moisture, and mechanical stress. Its precision is critical: any misalignment or defect could lead to increased vibration, noise, or even premature motor failure.
The design of motor end caps requires a careful balance between strength and weight. The choice of material, surface finish, and dimensional accuracy all impact the performance of the final assembly. Moreover, as washing machines are subject to varying loads and continuous operation, the end cap must maintain its integrity over thousands of cycles, making durability a paramount consideration.
Transfer die stamping is particularly well-suited for producing parts like motor end caps because it offers several advantages: high repeatability, excellent dimensional accuracy, and the ability to work with high-strength metals. This process involves a series of stamping operations performed in sequence, with a mechanical transfer system moving the workpiece from one station to the next. This seamless progression not only boosts production speed but also minimizes manual handling, reducing the risk of human error.
Transfer die stamping is an integrated stamping process that transforms metal sheets into finished components through a series of sequential operations. In the context of washing machine motor end caps, this method can include blanking, forming, bending, and final cutting. Here is an in-depth look at each step:
Detailed Explanation of the Transfer Die Stamping Production Process
The production process begins with the blanking operation, where a flat metal strip or coil is fed into the stamping press. A high-precision punch and die system cut out a blank—the raw shape of the end cap. The blank must be of uniform thickness and free from imperfections, as any defect at this stage can compromise the quality of the final product.
Once the blank is created, it is transferred automatically to the pre-forming station. Here, the blank undergoes initial forming operations. This stage might involve creating preliminary bends or curvatures that prepare the material for more complex shaping later on. The transfer mechanism is critical as it ensures that the blank is correctly aligned when it enters the next stage of the stamping process.
At this stage, additional dies and punches work in tandem to form the intricate features of the end cap. These may include creating flanges, reinforcing ribs, or precise contours that are necessary for the component’s function in the motor assembly. The design of these dies is highly specialized; they must account for the material’s springback, ensuring that the final geometry adheres to strict tolerances.
After the major forming operations, the part may have excess material or flash that needs to be trimmed. The stamping press, equipped with a dedicated trimming die, removes these unwanted sections, refining the part’s edges. The cutting operations are performed with extreme precision to ensure that the component meets both aesthetic and functional requirements.
As the part completes the stamping sequence, it is inspected using automated optical measurement systems. These systems check for dimensional accuracy, surface finish, and structural integrity. Any part that does not meet the quality standards is rejected or recycled. This final quality control step is essential in ensuring that only components that meet strict industrial standards are passed on for assembly into the washing machine motor.
The performance of a washing machine motor end cap largely depends on the materials used and the design specifications. Typically, manufacturers choose materials such as low-carbon steel or aluminum because these materials offer a good balance of strength, malleability, and cost-effectiveness. The material must also be capable of withstanding repeated mechanical stresses and the thermal cycles encountered during motor operation.
Design considerations include the following:
Dimensional Accuracy
The end cap must be produced with tight tolerances. In the transfer stamping process, the use of precise dies ensures that every component is uniform in size and shape, which is critical for proper motor assembly.
Surface Quality
The surface finish of the end cap affects both its performance and its appearance. A smooth surface can help reduce friction and wear when the component is assembled, thereby enhancing the overall reliability of the motor.
Mechanical Strength
The part must be robust enough to support the mechanical loads imposed by the motor’s operation. Reinforcements such as ribs or gussets might be integrated into the design to boost structural integrity without significantly increasing weight.
Thermal Properties
Since the motor generates heat during operation, the end cap may also play a role in heat dissipation. Materials with high thermal conductivity can help disperse heat more effectively, thus contributing to the longevity of the motor.
Material Selection and Design Considerations
Equipment and Machinery Used in Transfer Die Stamping
The transfer die stamping process utilizes high-speed stamping presses equipped with multiple stations and a variety of dies and punches. Some of the key components of the production line include:
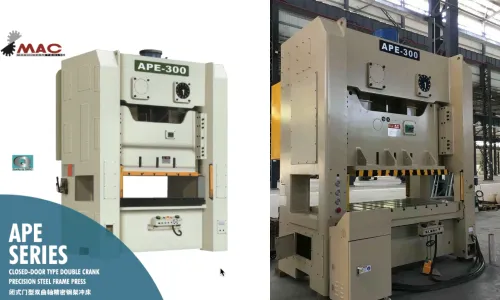
Stamping Press
Modern stamping presses are designed for high productivity and precision. They can perform multiple operations in a single cycle, reducing production time and energy consumption. Hydraulic and mechanical presses are commonly used in stamping applications, each offering distinct advantages depending on the material and design requirements.
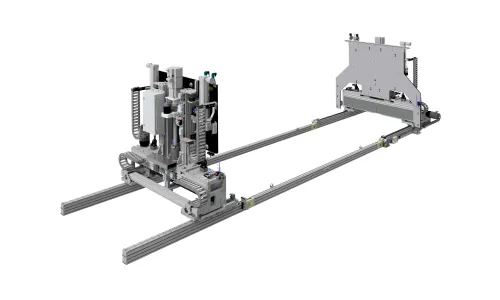
Transfer System
This automated system moves the workpiece from one station to the next. The transfer system is programmed to handle the precise positioning of the part, ensuring that each stamping operation is aligned correctly. The use of robotics and automation in the transfer system minimizes human intervention, leading to higher consistency and throughput.
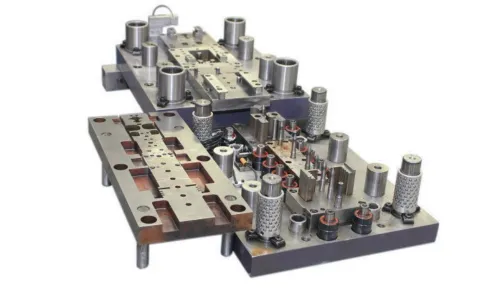
Tooling and Dies
The design and manufacture of the stamping dies are critical to the success of the process. Dies must be fabricated from high-quality, wear-resistant materials to withstand the repetitive high-pressure operations. Advanced computer-aided design (CAD) and computer-aided manufacturing (CAM) technologies are employed to create dies that meet exact specifications.
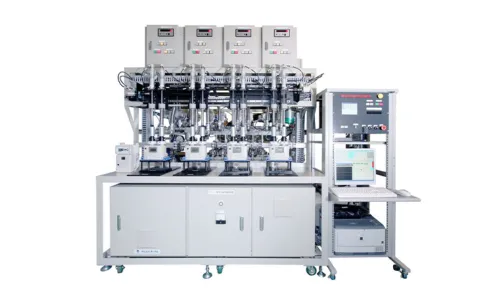
Inspection and Measurement Equipment
Quality control is an integral part of the production process. High-resolution cameras, laser measurement systems, and other automated inspection tools ensure that each component meets the required tolerances. These systems can detect even minor defects, allowing for immediate corrective actions.
Quality Control and Production Efficiency
One of the key benefits of the transfer die stamping process is the ability to maintain high production efficiency while ensuring that each component meets stringent quality standards. Quality control is integrated at every stage of the production process: