Modular Die Stamping Line For TV Back Panels
Modular Die Stamping Line for 55-inch TV Back Panels
Core Concept: Ditching Progressive Dies for Modular Flexibility
Traditional 12-station progressive dies offer high speed but come with drawbacks, complex maintenance, and inflexibility for custom designs. The modular die solution splits processes into independent dies + presses, cutting die , slashing changeover to 8 minutes, and excelling in:
- Complex 55-inch back panels (e.g., Mini LED cooling hole arrays)
- Mixed production of 32–75-inch models (10+ monthly changeovers)
- Small batches (50pcs+ for e-commerce exclusives)
Process Breakdown & Layout (55-inch Panel Example)
Process Split Principle: ≤30s per process, 40% simpler dies
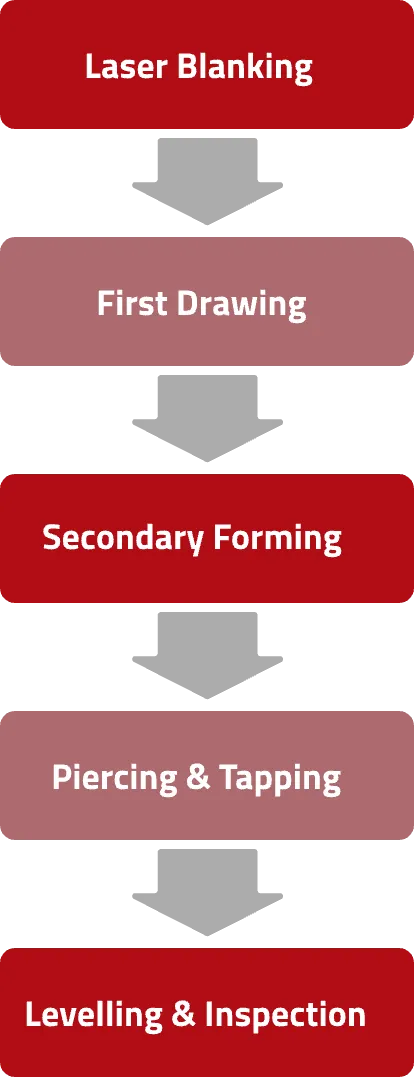
| Machine | Die Type | Key Parameters | Automation |
1. Laser Blanking | 6kW Fiber Laser Cutter | No-die (CAD-driven) | Cutting accuracy ±0.05mm, burr ≤0.03mm | AGV with vacuum suction |
2. First Drawing | 1600T Double-Acting Servo Press | Modular drawing die (with blank holder) | Depth 25mm, R8mm, blank holder force 50–150T adjustable | 6-axis robot + vision alignment |
3. Secondary Forming | 1000T Single-Acting Servo Press | Flanging & shaping die | 15mm flange, perpendicularity ≤0.8° | Robot arm + magnetic separator (anti-iron filings) |
4. Piercing & Tapping | 500T High-Speed Press (200spm) | Multi-hole modular die | φ5–φ12mm holes, positional accuracy ±0.1mm | Vibratory feeder + CCD inspection |
5. Levelling & Inspection | 300T Precision Leveller | Floating levelling die | Flatness ≤0.3mm/m | Laser thickness gauge + AI defect detection |

Layout: U-shaped tandem + buffer islands (25% space saving)
Key Equipment & Die Innovations
Laser Blanking Replaces Traditional Dies
Machine: Laser (4000×2000mm), AI path optimization
Advantages:
- Eliminates blanking die, saving cost model in tooling
- Supports any custom contour (rounded corners, partial hollowing)
- Scrap rate reduced from 6.5% to 4.2% (nesting algorithm optimization)
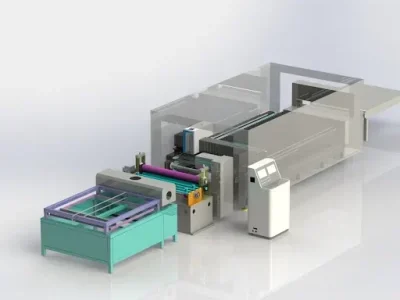
Double-Acting Press + Modular Drawing Die
Machine: APC(double-point, outer slide 0–300T blank holder force)
Die Design:
- Replaceable blank holder inserts (55→65-inch R-angle change in 20 minutes)
- Built-in coolant circulation (±2℃ temperature control, prevents thermal deformation)
Process: Drawing speed 80mm/s (crack rate 0.2% vs. progressive die’s 0.8%)
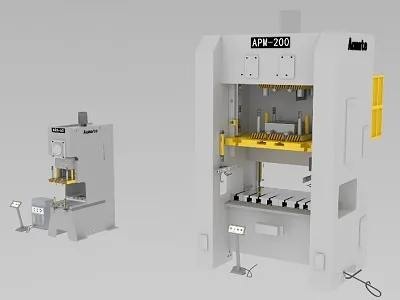
Quick-Change Piercing Unit
Die: Drawer-style structure (one-click plug-and-play), 55→65-inch die change in 8 minutes
Anti-Error: Die ID chip auto-matches NC program, 0 misinstallation
Efficiency: 180pcs/hour (progressive die: 240pcs/hour, but changeover time 1/5)
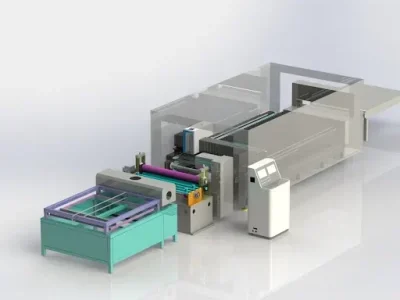
Application Scenarios & Upgrades
Ideal for:
Small/medium TV manufacturers
Annual capacity <1M units
ODM/OEM factories
Multi-brand, multi-model production
New display R&D
E.g., OLED curved back panels
Technology Upgrades:
Die Cloud Platform
7-day new die development (vs. 21 days traditionally)
Process Integration
Laser welding integrated into forming press, reducing 3 handling steps
AI Cracking Prediction
30-minute advance warning via drawing pressure curves (92% accuracy)
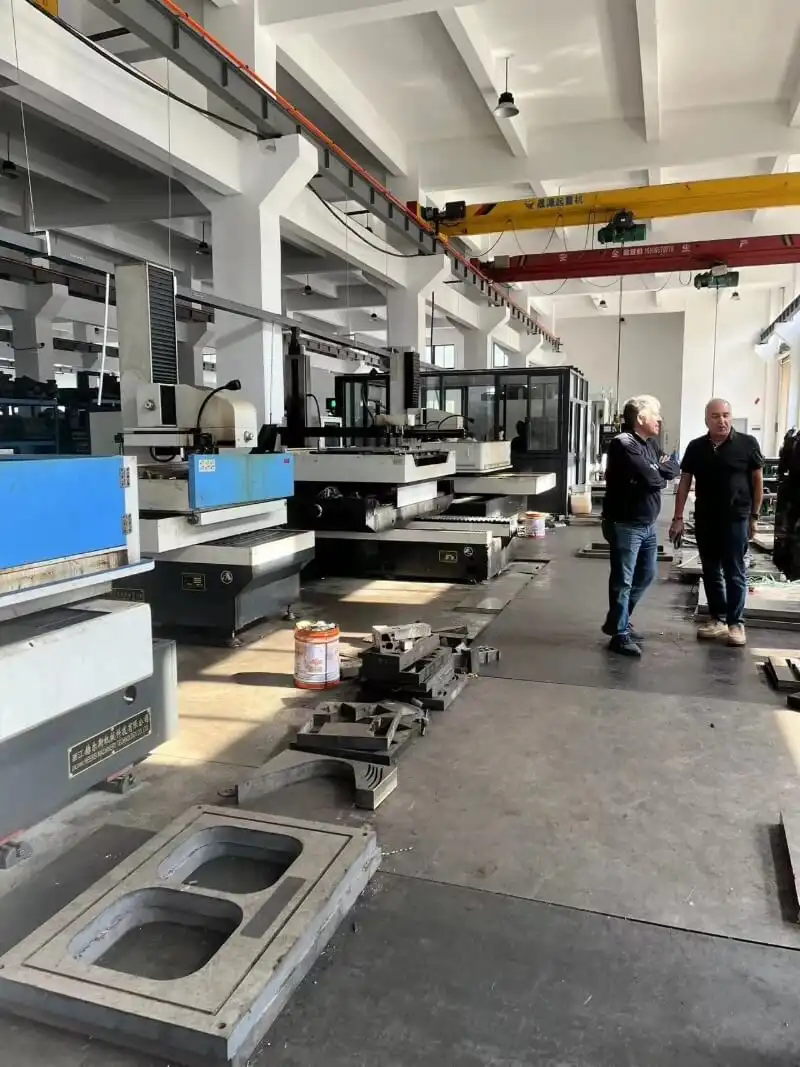