Stator-Rotor High-Speed Punch
Stator-Rotor High-Speed Punch
Our computer controller is designed specifically with the punching proces in mind. Its ease of use and power are derived from a rich set of special functions, simple interface, mode setting in checklist form, error code display, and ample memory capacity. Specifically, the features include
- Fair Oaks' own PLC-SI Controller with exclusive software.
- Selections for stop angle in inching mode.
- Digital setting for stroke speeds.
- Lot "A", "B" control for auto-stacking of rotor & stator laminations.
- Special Lot "C" Control for punching rotor holes of different sizes.
- Sufficient memory to allow up to 30 sets of diesetting data.
- Convenient mode setting operation.
- Self-diagnostic function, error code display, and indicator lights.
Description
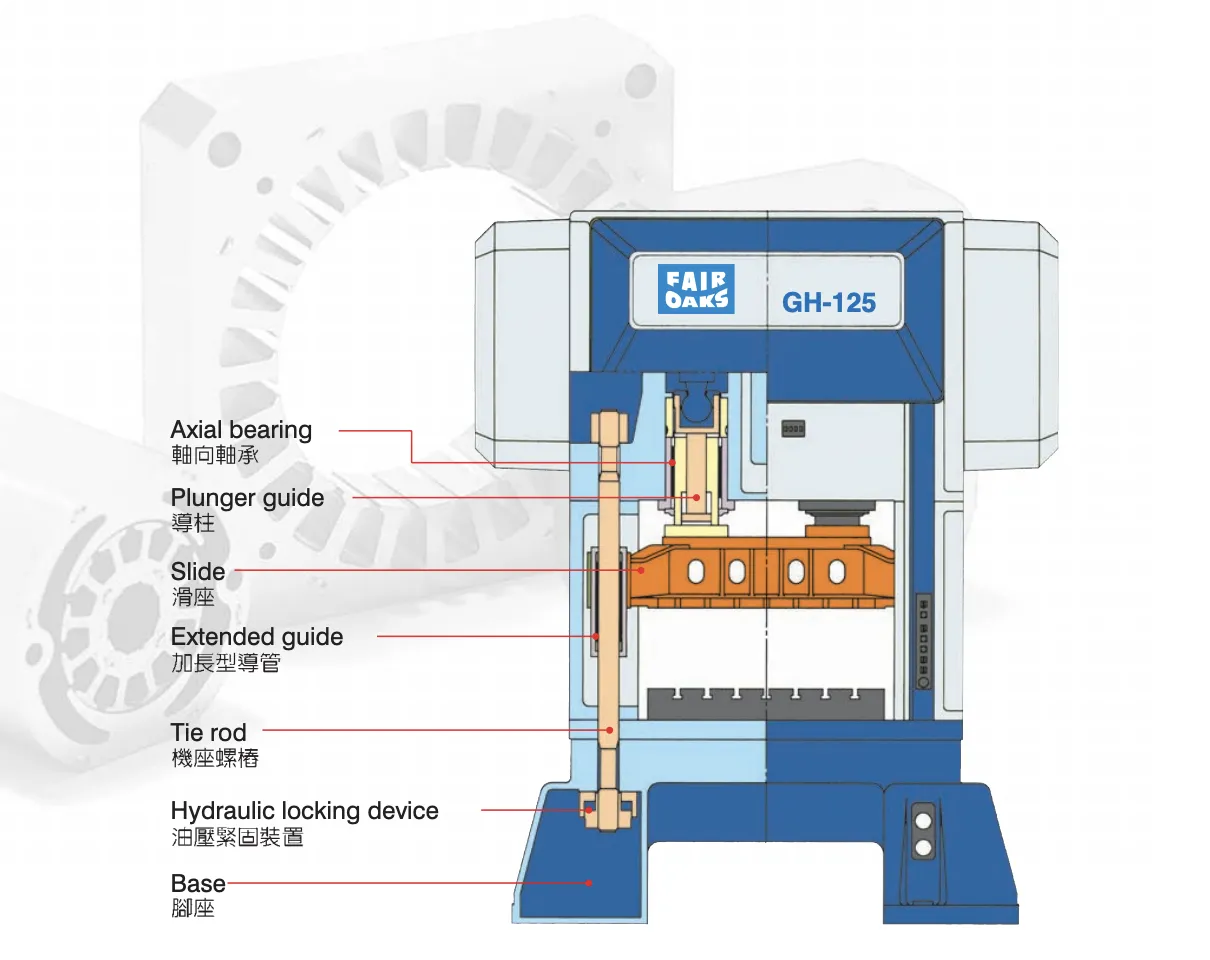
MACHINE FEATURES
FRAME
- Manufactured from high tensile cast iron, stress relieved for maximum rigidity and long term accuracy.
- The frame structure is designed by means of “Computerized finite element analysis”. It provides optimum design for frame strength and strain.
- The frame is tightened by tie-rods, incorporating with hydraulic preload on structure for giving added rigidity.
MINIMUM VIBRATION, MINIMUM NOISE
- Outstanding dynamic balancing design reduces vibration and noise to a minimum.
PRECISION MAIN SHAFT
- Manufactured from Nickel Chrome Molybedenum alloy steel, hardened and precision ground.
HIGH POSITIONING ACCURACY
- Sensitive separated type clutcn and brake assure high positioning accuracy and maximum safety guard.
- Plunger guides & slide guides utilize clearance free axial bearings.
- Preloaded tie-rods employed on slide guide for high rigidity, incorporating with extended guide for highly dynamic and static accuracy, service life of punch dies can be greatly upgraded.
LUBRICATION SYSTEM
- Employs a forced lubrication with cooling system to minimize thermal strain of machine frame, upgrade stamping quality and extend service life of the machine. The lubrication system is provided with a pressure detection device.
Product model
GH-30
• 30 tons press capacity
• 600x450 mm bolster area
• 11kw motordrive
• 600x450 mm bolster area
• 11kw motordrive
GH-45
• 45 tons press capacity
• 750x550 mm bolster area
• 15kw motordrive
• 750x550 mm bolster area
• 15kw motordrive
GH-60
• 60 tons press capacity
• 950x650 mm bolster area
• 19kw motordrive
• 950x650 mm bolster area
• 19kw motordrive
GH-80
• 80 tons press capacity
• 1100x750 mm bolster area
• 22kw motordrive
• 1100x750 mm bolster area
• 22kw motordrive
GH-125
• 125 tons press capacity
• 1200x850 mm bolster area
• 37kw motordrive
• 1200x850 mm bolster area
• 37kw motordrive
GH-220
• 220 tons press capacity
• 1700x950 mm bolster area
• 45kw motordrive
• 1700x950 mm bolster area
• 45kw motordrive
GH-300
• 300 tons press capacity
• 2000x1000 mm bolster area
• 45kw motordrive
• 2000x1000 mm bolster area
• 45kw motordrive
Optional Equipment
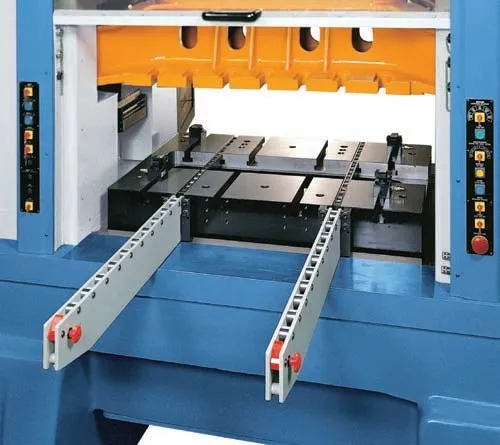
QUICK DIE CHANGE EQUIPMENT
1. Hydraulic die lifter.
2. Die arms (Pre-rollers).
3. Hydraulic die clampers for upper die.
4. Hydraulic die clampers for lower die.
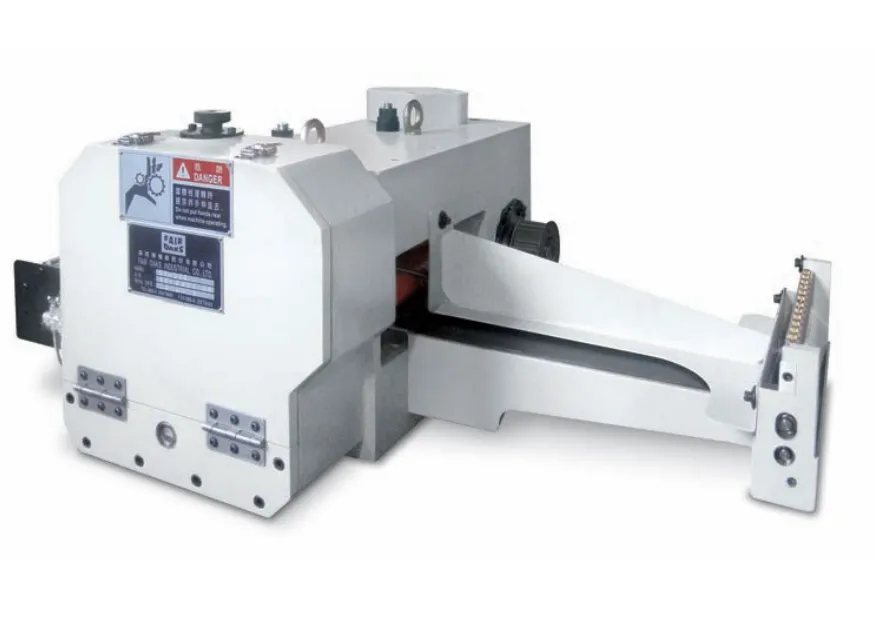
HI-SPEED FEEDER
Standard Equipments:
1. Material lubrication device.
(With flow regulator)
2. Gear 4 pcs. (Teeth numbers as specified)
3. Extended material support.
4. Material end sensor. (DC24V NPN)
5. Pneumatic material clamping device.
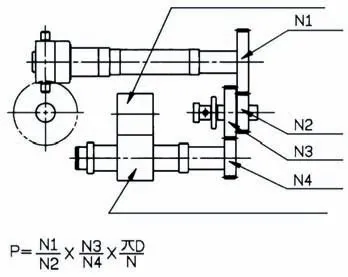
GEAR-CHANGE TYPE HIGH SPEED FEEDER
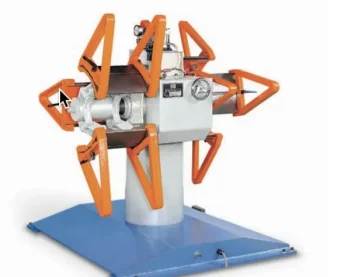
DOUBLE HEAD UNCOILER
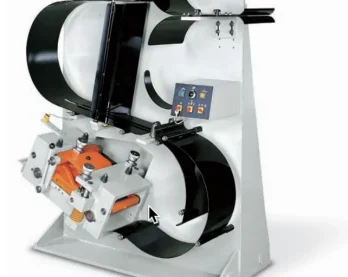