Kitchen Sink Production Line
Kitchen Sink Production Line
This production line contains a decoiler for decoiling raw material, an auto-feeder and a shearing machine for cutting material, a hydraulic press for deep drawing of sinks, cutting and trimming of edges, and a polishing machine for polishing sink surfaces.
- Suitable for sinks of various shapes
- High production efficiency
- Fully automatic and semi-automatic optional
Description
Product Cases
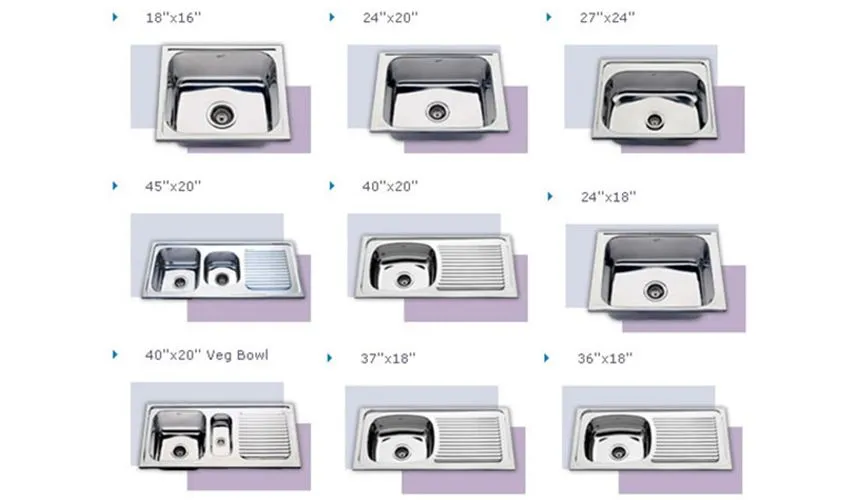
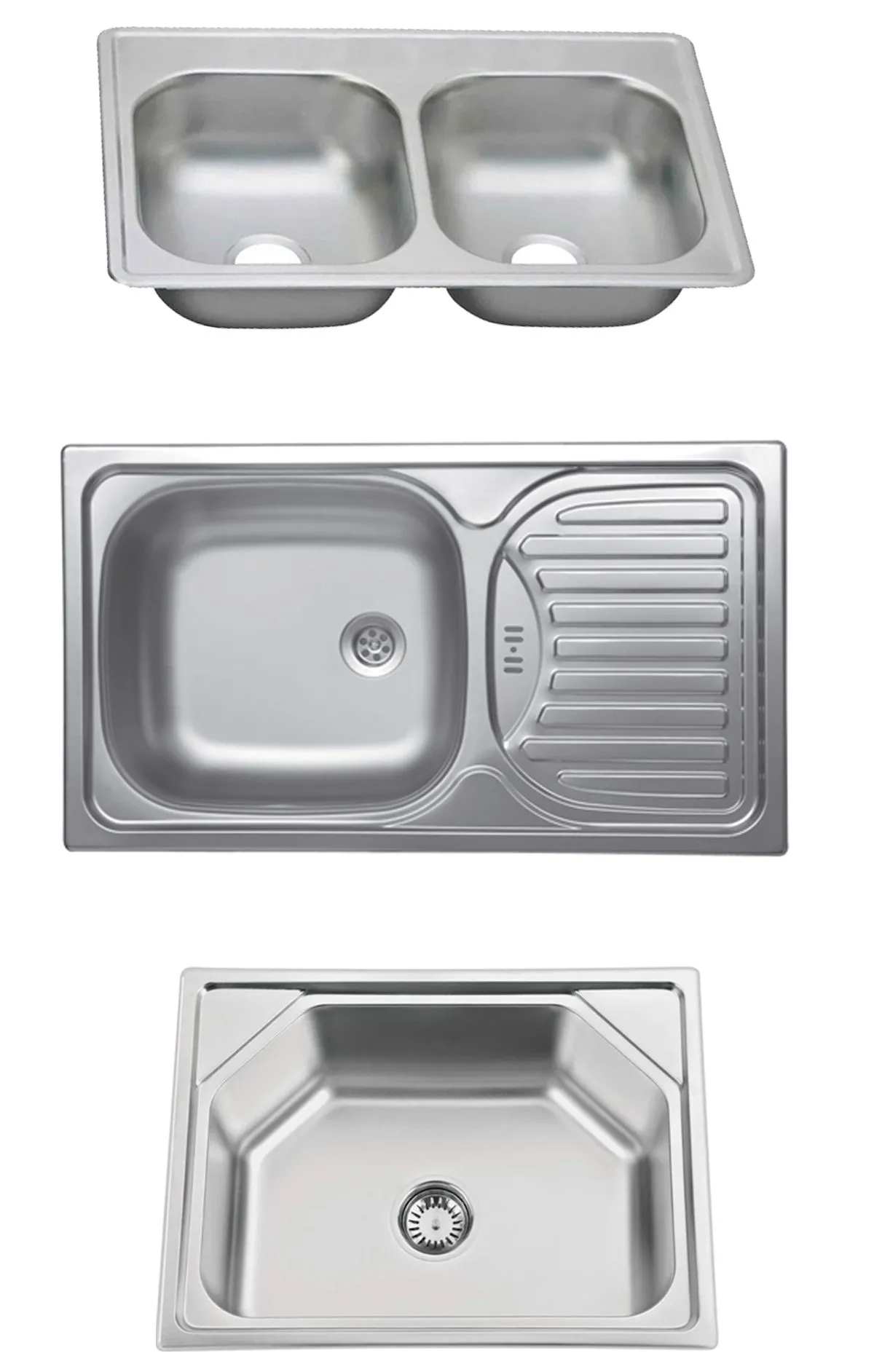
High-Quality Production: SMAC’s kitchen sink production line ensures precision and superior quality with every unit.
Stable Capacity: Designed for consistent, high-volume production, our line guarantees stable output and efficiency.
Advanced Technology: Utilizing the latest machinery and automation, our production line delivers flawless performance and reliable results.
Durable & Functional: Each sink produced is crafted to meet stringent quality standards, ensuring durability and long-lasting functionality.
Efficient Manufacturing: SMAC’s streamlined production process reduces lead times and maximizes production efficiency, making it the perfect choice for large-scale manufacturing.
The Kitchen Sink Production Line involves a series of carefully orchestrated steps to transform raw materials into finished sinks. Below is an overview of the key processes:
Material Cutting: The production starts with cutting large metal sheets (typically stainless steel or corrosion-resistant materials) into the required sizes using shearing machines. These metal sheets form the base material for the sink.
Deep Drawing: The sheets are then subjected to deep drawing using a hydraulic press. This process shapes the metal into the basic sink bowl shape, creating the necessary curves and depth.
Stamping Drain & Overflow Holes: Using the power press, drain and overflow holes are stamped precisely in the right positions on the sink, ensuring both functionality and a high-quality finish.
Edge Forming & Trimming: The edges of the sink are formed and trimmed using the hydraulic press for a smooth, clean finish. This is crucial for both the appearance and the installation process.
Polishing: The sink undergoes multiple polishing steps using bottom polishing machines, four-side polishing machines, and manual surface grinding machines. This removes imperfections, enhances the sink’s shine, and gives it a smooth, clean surface.
Assembly: Any additional features, such as mounting brackets or accessories, are added at this stage, ensuring the sink is fully functional.
Quality Control & Inspection: Each sink is carefully inspected to meet quality standards. This includes checking for correct hole placements, smoothness of edges, and overall finish.
Workflow
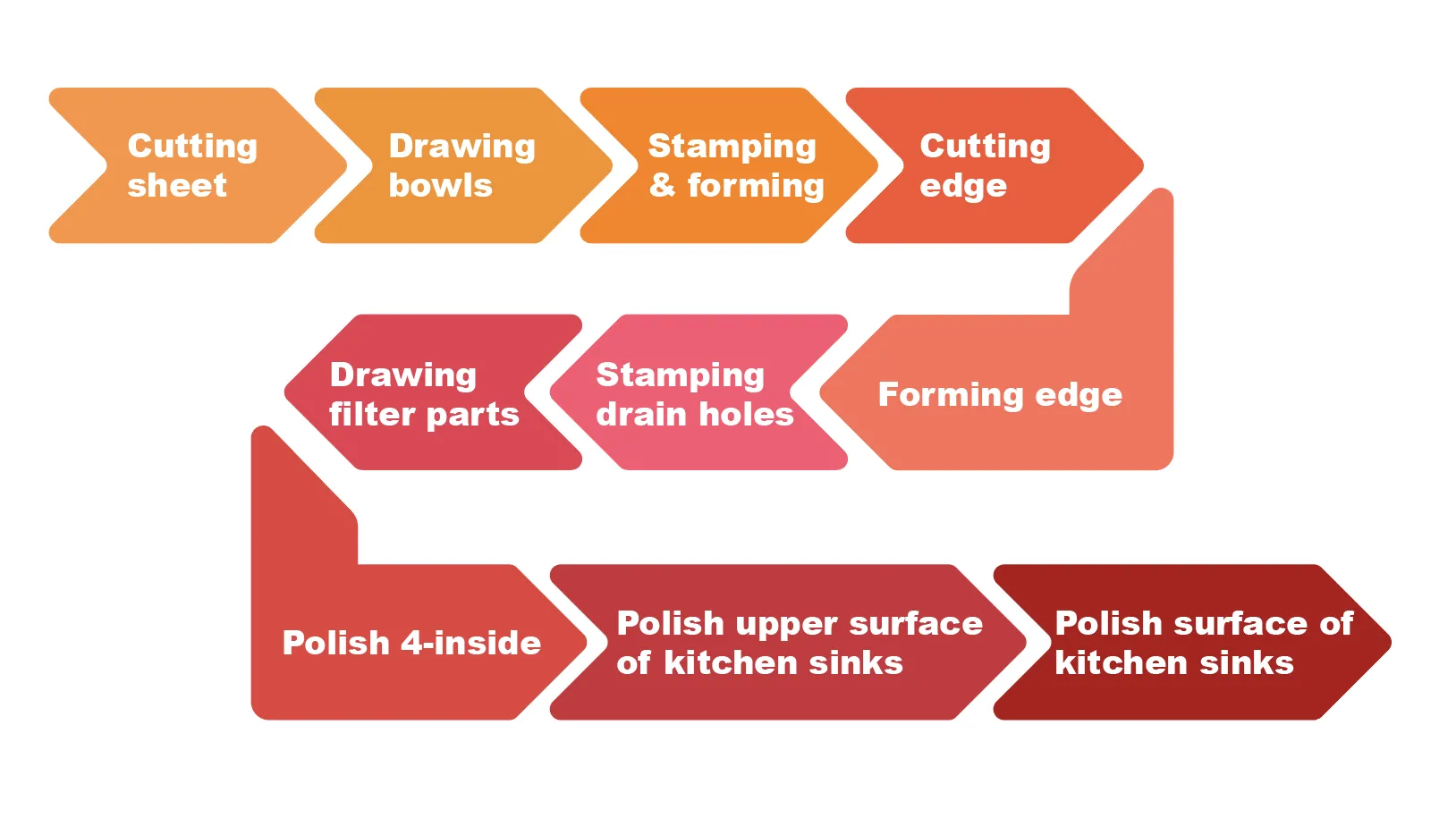
Main Equipment
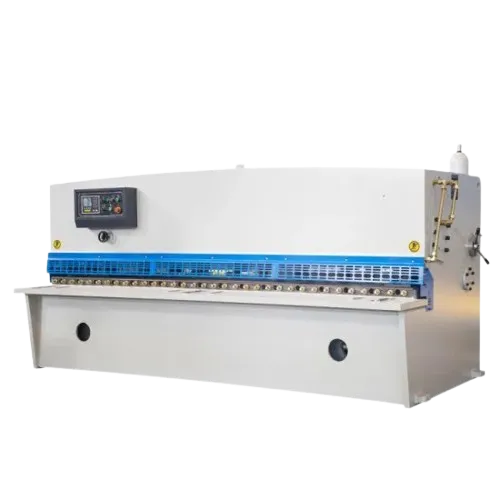
Shearing Machine
Cutting and shaping metal sheets to the required size for subsequent processing. cut large metal sheets (typically stainless steel or corrosion-resistant materials) into specified sizes for the sink’s main body.
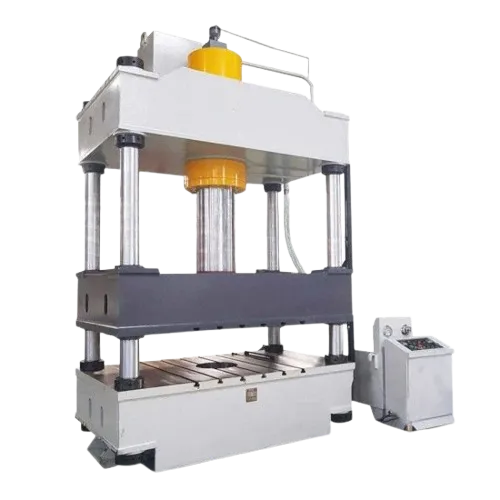
Hydraulic Press Machine
Based on your sink dimensions (4 types in total), we recommend selecting the press machine capacity according to the largest dimensions.
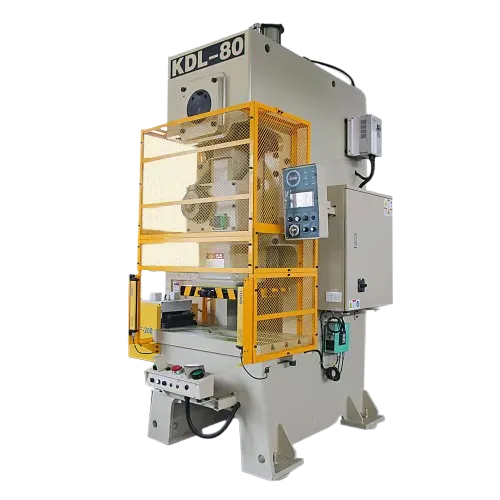
Power press machine
Key functions include:Forming Sink Shape: Stamps and molds metal sheets into complex sink shapes, like deep bowls and curves. Stamping Drain & Overflow Holes: Precisely stamps drain and overflow holes for functionality. Edge Forming: Shapes sink edges for a clean, smooth finish and safe installation. High-Speed Production: Enables fast, efficient stamping for large-scale manufacturing, ensuring consistent quality and reducing production time.
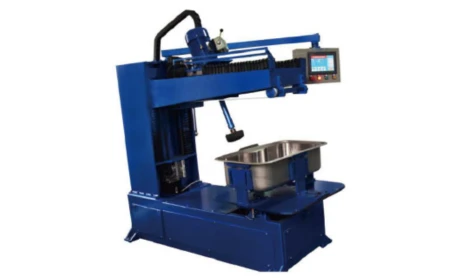
Tank bottom polishing machine
Used for efficiently polishing the bottom of the sink to ensure a smooth, shiny, and flawless surface.
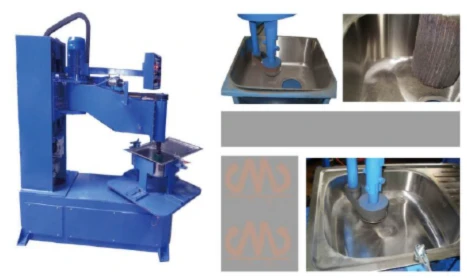
Four side polishing machine
Lorem ipsum dolor sit amet, consectetur adipiscing elit. Ut elit tellus, luctus nec ullamcorper mattis, pulvinar dapibus leo.
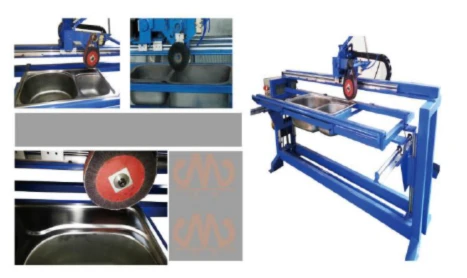
Manual surface polishing machine
Used for fine grinding of the sink’s surface to remove minor imperfections and improve smoothness.
Hydraulic Press Machine Parameter Table
Item | Unit | YQ27 -63 | YQ27 -100 | YQ27 -200 | YQ27 -315 | YQ27 -500(1) | YQ27 -500(2) | YQ27 -630 | YQ27 -1000 | ||
Nominal Force | KN | 630 | 1000 | 2000 | 3150 | 5000 | 5000 | 6300 | 10000 | ||
Return Force | KN | 180 | 260 | 480 | 630 | 1000 | 1000 | 1250 | 1250 | ||
Cushion Force | KN | 200 | 500 | 800 | 1250 | 1000 | 1600 | 2500 | 3000 | ||
Max. pressure of liquid | MPa | 25 | 25 | 25 | 25 | 25 | 25 | 25 | 25 | ||
Stroke | Slide | mm | 450 | 700 | 710 | 800 | 900 | 900 | 1000 | 1400 | |
Cushion | mm | 180 | 300 | 250 | 300 | 350 | 300 | 400 | 350 | ||
Max. Daylight | mm | 900 | 1000 | 1120 | 1250 | 1500 | 1500 | 1600 | 2300 | ||
Slide speed | Descent | mm/s | 120 | 150 | 100 | 100 | 140 | 100 | 100 | 100 | |
Pressing | mm/s | 11-15 | 20 | 6-15 | 6-12 | 5-15 | 8 | 6-14 | 13 | ||
Return | mm/s | 130 | 80 | 80 | 60 | 70 | 90 | 65 | 60 | ||
Table Dimensions | L-R | mm | 560 | 720 | 1000 | 1250 | 1400 | 2200 | 2600 | 2500 | |
F-B | mm | 500 | 580 | 900 | 1120 | 1400 | 1400 | 1750 | 2000 | ||
Cushion Dimensions | L-R | mm | 310 | 470 | 800 | 900 | 1100 | 1700 | 1950 | 2000 | |
F-B | mm | 300 | 430 | 630 | 800 | 1100 | 900 | 1200 | 1500 | ||
Height of table above Floor | mm | 750 | 750 | 500 | 600 | 500 | 500 | 500 | 0 | ||
Total Power | KW | 22 | 22 | 45 | 45 | 45 | 90 | ||||
Total Weight | Kg | 4200 | 6500 | 14200 | 18000 | 29500 | 41000 | 77000 | 102000 | ||
Overall Dimensions | L-R | mm | 1420 | 1960 | 2698 | 3018 | 4120 | 4750 | 5222 | 5800 | |
F-B | mm | 1265 | 1620 | 2530 | 2530 | 3600 | 3800 | 3785 | 6050 | ||
Height above Floor | mm | 2698 | 3250 | 4110 | 4560 | 5545 | 5545 | 5970 | 8098 | ||
Depth below Floor | mm | 300 | 800 | 1000 | 1200 | 1000 | 1400 | 2400 | |||
Form of frame | four column | four column | four column | four column | four column | four column | four column | four column |